Purveyors of Custom Assembly & Test Machines
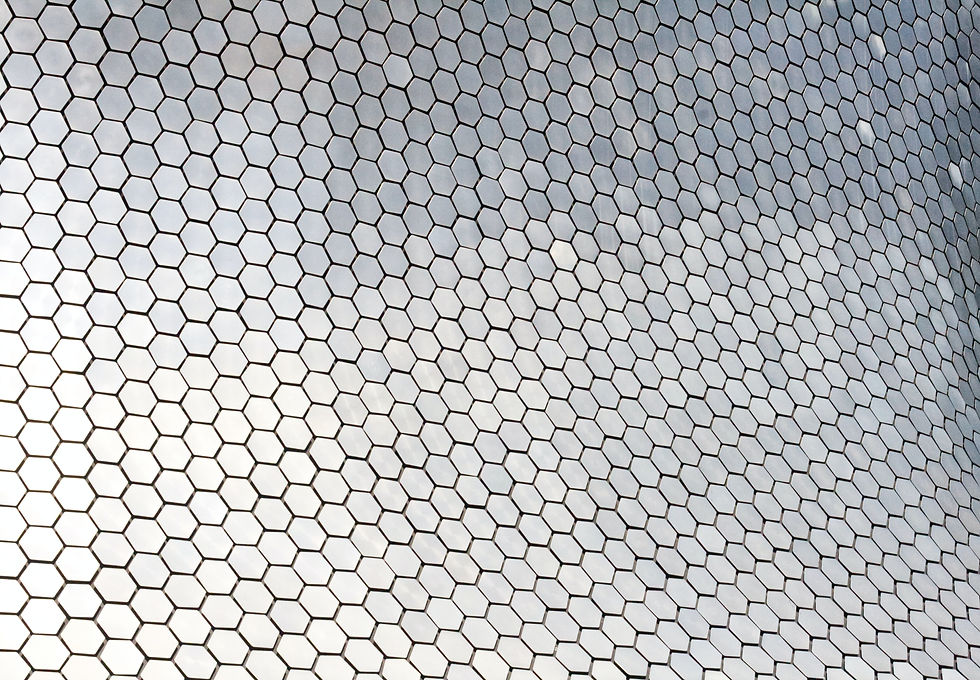
FULLY-AUTOMATED & SEMI-AUTOMATED ASSEMBLY SOLUTIONS
PURITAN designs, builds, and integrates custom assembly and automation systems, creating each one using multiple assembly processes and often integrating end-of-line testing.
Because each system implements a unique manufacturing process, addressing our customer's needs and specifications, we have developed experience in numerous areas:
Semi-Automated Assembly
-
single station assembly
-
multi-station work cells
-
synchronous and non-synchronous conveyors
-
dial tables
Fully Automated Assembly
-
non-synchronous conveyors
-
synchronous indexing tables
and conveyors -
robotic integration
Below are a few examples of equipment built for the world's leading manufacturers:

Fuel Line Forming, Assembly & Test
This Japanese company produces a high quantity of fuel lines and related components.
The company approached Puritan to produce a dial table-based assembly machine to increase throughput, accommodating its growing business.
Blank and straight fuel lines, as well as end-connectors, are loaded into nesting on the dial table.
In one revolution of the dial table, the end-connectors are attached to the fuel line, the fuel line is formed (shaped) via heated forms, and the final assembly is leak-tested prior to removal from the machine.

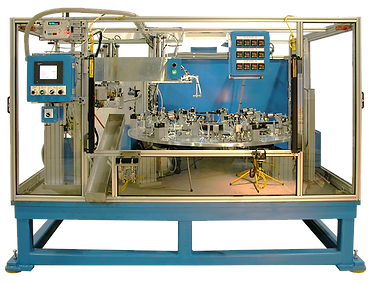

Semi-Automated Fuel Line Assembly & Test Machine

This machine inserts two fuel connectors into a Nylon fuel line and leak tests the final assembly.
Each component is manually loaded into the tooling nest and the assembly process is completed in a single cycle.
While in the nest, a manifold and plug is presented to either end of the assembly to interface to the leak test apparatus.
An air pressure leak test is performed and the part released from the tooling to be removed by the operator.
This Japanese client enforces strict ergonomic regulations for assembly machines and the safety of their operators.
Typical light curtains and a cycle-start palm button are incorporated as well as an adjustable-height machine table.
PURITAN has built over twelve assembly/test machines and fixtures for this client in recent years.
3M Blood Filtration System Housing - Adhesive Applicator
When 3M required a glue bonding process for a blood filtration system housing, they contracted PURITAN to design and build a semi-automated bonding machine equipped with a medical-grade Medi Cure MC300 Ultra Violet cure system.
The high strength structural adhesive is automatically applied to the assembly in a controlled quantity.
The medical assembly is manually nested by the operator, adhesive is automatically applied, and then the part is automatically transferred to the curing station for eventual removal from the machine.
This assembly equipment is operated in a clean-room environment.

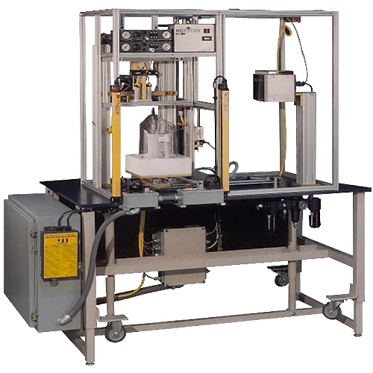

Semi-Automated Fuel Line Assembly & Test Machine
.png)

This German client manufactures fuel line assemblies and required a machine that would form a plastic fuel line by heating and cooling various bends that are shaped in the nest on a high-speed indexing dial table.
Each nest on the table houses various electric heaters and temperature sensors that require connection and disconnection during the rotation of the table. This is performed using a retractable bed-of nails-type electrical interface that is maneuvered by pneumatic cylinder.
A pick & place unit moves the final assembly to a final station where it is pressure-leak tested and paint-marked to verify quantity.
The cycle time is approximately fifteen seconds.
Wheel Hub Stud Insertion & Test Machine
This client required a machine to insert splined and threaded wheel studs into hubs while monitoring the force and stroke required to correctly insert the stud into the hub.
Studs are sorted in a vibratory bowl and brought to the machine via a linear slide. Once at the machine, the stud is ‘blow-piped’ into the blank hub.
An indexer rotates the hub after each stud is inserted while a precision instrument monitors the force and stroke using a LVDT and precision load cell.
An air-over-hydraulic intensifier is utilized to produce the press forces required.
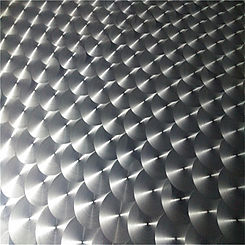

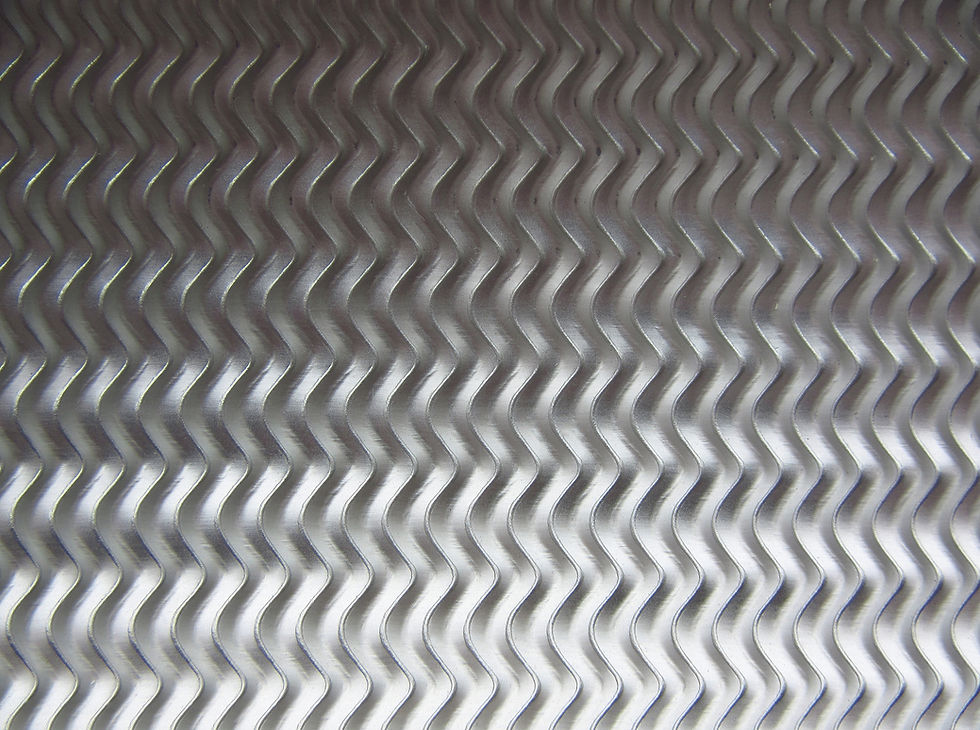
And Many More...

This robotic assembly machine pressed multiple (3) snap-in nuts into an automotive bezel using a SCARA Intelligent Actuator Robot.
Part handling is performed using vibratory feeders and an indexing dial table to complete the process.
Each assembled part is gauged to ensure correct installation of nuts using fiber optic sensors.
This Michigan-based customer has commissioned Puritan to design and build over twelve assembly machines in past years.
This machine performs the following assembly steps on an automotive electrical connector:
-
insert silicone seal
-
insert locking spacer
-
insert connector mounting clip
All components are checked for correct placement and orientation with a sub-two second cycle rate (complete assembly and gauge time).
All components are fed via vibratory bowls and inline feeders to an indexing dial table.
The ‘good part’ chute is equipped with a diverter and counting system that can fill two dunnage containers to predetermined quantities.


This machine performs the following assembly steps on a automotive electrical connector:
-
insert large silicone seal
-
insert O-ring
-
insert long mounting fastener (bolt)
-
press in captive fastener nut
All components are checked for correct placement and orientation with a sub-two second cycle rate (complete assembly and gauge time).
All components are fed via vibratory bowls and inline feeders to an indexing dial table.
The machine assembles an adjustable locking bolt, pivot pin, captive-nut, and Zinc corrosion inhibitor gasket to complete an automotive door hinge.
The machine is fed by multiple vibratory bowls and inline feeders, and the assembly process is performed on an indexing dial table.
This customer is located in Battle Creek, Michigan and is a major Tier 1 automotive manufacturer.
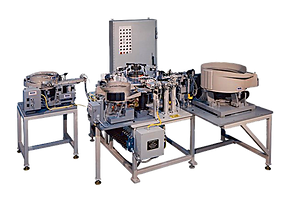

This client required an assembly machine to insert a fastener (machine screw) into a plastic mounting bracket for an automotive component.
Both the bracket and fastener are fed to the indexing dial table via vibratory bowls and inline feeders.
At the dial table, the screw is inserted and then gauged for correct length of screw and depth.
This Fowlerville Tier 2 manufacturer has commissioned us to design and build over twelve assembly machines and fixtures in recent years.